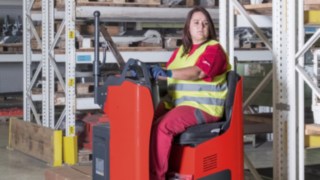
Second stage launched
15 Jan 2018
New driver's seat and stand-on platform trucks from Linde Material Handling offer enhanced comfort, safety, and performance
Last year, Linde Material Handling launched a new product family of driver's seat and stand-on platform pallet trucks and double stackers. Following the introduction of trucks with a lateral or frontal stand-on platform, models with a lateral driver’s seat are now being launched on the market as a second step. Common to all these trucks is their high traction force and stability, an option of either lead-acid or lithium-ion batteries, and the innovative TipControl for handling driving and lifting functions. In addition, they all allow for the flexible arrangement of operating elements.
The new trucks include Linde T20 R and T 25 R pallet trucks with 2.0 and 2.5 tons load capacity respectively, Linde D12 R double stackers with 1.2 tons load capacity and Linde L14 R and L16 R pallet stackers with 1.4 and 1.6 tons load capacity, all of which feature a new chassis width of 820 millimeters. In addition, Linde T20 SR and T25 SR pallet trucks are available with a lateral stand-on platform which can lift 2.0 and 2.5 tons respectively, and both have a chassis width of 790 millimeters.
When speaking with logistics managers, it becomes evident that vehicle ergonomics is of crucial importance, since in many companies the motivation and well-being of drivers are decisive success factors in ensuring high productivity. The seat in an industrial truck plays a key role in offering the driver a comfortable place from which to carry out tasks. In the new trucks, it is available in two versions: with a fabric cover as standard and optionally with hard-wearing imitation leather. To ensure that the driver can adjust the seat to accommodate his body as ergonomically as possible, the backrest tilt, distance to the control panel and weight can be adjusted by means of levers positioned underneath the seat. The optionally available seat heating system provides additional comfort and protects the driver’s health at temperatures below zero in refrigerated warehouses. A sturdy, padded handle and an adjustable base plate allow comfortable entry into the vehicle. During work, the padded armrest, easy-to-reach “TipControl” lever, steering wheel, and padded knee protection offer a high level of comfort and help reduce fatigue.
The TipControl is a newly developed feature – a handle and control lever rolled into one which can be installed on the right or left of the operation panel in many models. The operator can control the driving and lifting functions precisely and simultaneously via thumb and index finger. The switches are easy to operate even when wearing gloves, with the driver’s wrist supported by a height-adjustable armrest. The large, multi-function color display shows all important operating conditions, such as the battery’s state of charge and the operating hours remaining until the next service check is due. If the optional Linde Load Management assistance system is installed, the driver also knows the weight acting on the load arms and the maximum height to which the current load can be lifted.
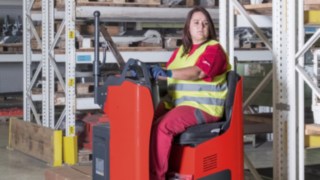
Common to all new Linde trucks with a lateral driver’s seat is their high traction force and stability, an option of either lead-acid or lithium-ion batteries, the innovative TipControl for handling driving and lifting functions and the flexible arrangement of operating elements.
Safety through numerous functions
Three autonomous braking systems provide efficient driver protection in various situations: The truck brakes automatically as soon as the driver releases the drive switch or leaves the area of the dead man’s switch. The third option is the emergency stop button. It can be reached quickly from anywhere, shuts down all electric circuits, and activates the electromechanical brake. The special free-swinging suspension of the load arms guarantees high traction even on rough ground. It ensures that all four wheels are equally supported at any time so that the truck is perpetually in a stable position.
The seating position, situated at a 90° angle to the direction of travel, provides a good view while driving forward and in reverse. This means that the driver can confidently steer the truck past racks and pallets or during longer distances through gates and over ramps. The optionally available panorama mirror for the driver’s seat trucks makes even the last blind spot around the vehicle visible.
Speed as desired
Performance and energy consumption are proportional to each other: The higher the performance, the more energy is consumed. For this reason, the new trucks allow the presetting of maximum travel speeds with and without load. This means that customers can make their own decisions about truck configuration. Possible values are between 8 km/h and 12 km/h, and changes can be made at any time via the service settings. To increase the operating life of the forks and avoid ground contact, for example on ramps, the forward speed can be reduced to 6 km/h when driving with lowered forks.
Versatility is the key
As operating conditions differ from company to company, most logistics managers want trucks that can be flexibly adapted. Linde’s new driver’s seat trucks offer all the necessary prerequisites for this. One example is the wide range of batteries on offer: Capacities of between 345 Ah and 500 Ah are available in the case of lead-acid batteries, which have all been optimized for lateral battery change: Metal rollers in the battery trough accelerate the replacement process, and the lever and spring ensure ergonomic locking and unlocking. Alternatively, Li-ION batteries are available, which are perfectly integrated into the vehicles and are recommended for intensive use in two- or multi-shift operation. Fast charging and intermediate charging – optionally via a lateral quick charging access – increases availability and eliminates the need for battery change as well as maintenance and servicing work. Three different charger sizes – 90A, 160A and 225A – reduce the time required for a full charge cycle to just one and a half hours, depending on the battery size. Li-ION batteries are particularly efficient for use in cold storage applications, as the low temperatures do not adversely affect the capacity or operating life.
The functional range of the trucks can be expanded as needed through numerous other equipment options: These range from a pre-installed 24V connection for data terminals to warning lights for increased visibility in cluttered areas, as well as the connect fleet management solution connect featuring the modules “access control” for controlling truck access, “crash detection” to reduce damage or “usage analysis” for optimized fleet utilization.
The intelligent arrangement of the components in the chassis ensures fast servicing. And thanks to the reduced number of components, for example, minimal cabling, maintenance intervals are now required after only around 1,000 operating hours.