Optimizing Logistics at Madi Ventura’s Brownfield Site
Fertile Ground for Healthy Growth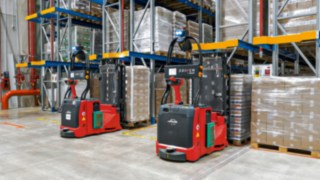
Italian company Madi Ventura has been a key player in the world of nuts and dried fruits for more than 80 years. Recently, they worked with Linde MH to overhaul and future-proof intralogistics at the main site near Milan; this included implementing flexible, scalable automation solutions in the form of automated pallet stackers and narrow aisle trucks.
Whether in muesli and desserts, or as a healthy snack, nuts and dried fruits have been popular around the world long before superfoods became a thing. At the same time, the industry is well aware of the ongoing growth in health consciousness among the population, as Giuseppe Calvini, Production Manager at Madi Ventura confirms: “Our revenue has grown by 25 percent in the last decade alone”. The Italian producer and importer is headquartered in Chieve, just an hour’s drive from Milan, where it handles more than 18,000 tonnes of products every calendar year, a trend which is rising sharply. Calvini summarizes what this means: “We had no choice but to hugely expand our production area.” Obviously, that also involved rethinking some areas of intralogistics.
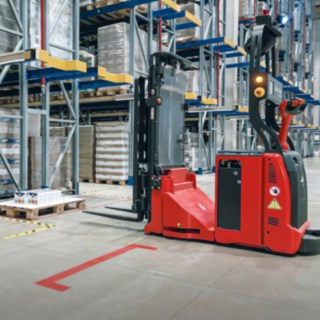
A Hard Nut to Crack
When Madi Ventura approached Linde MH, they had a detailed requirements specification: more production space, more warehouse space for their stock, and more efficient, automated logistics, with the additional requirement that this could be easily scaled up if necessary. “We were looking for a supplier who understood our requirements and could give us the necessary support in every phase, from analysis right through to full-scale operation,” is how Logistics Manager Simone Gedda sees it. No mean feat, particularly since the newly designed, automated finished parts warehouse would also have to be able to interact with other sectors; in other words, operating areas where operator-controlled industrial trucks and pedestrians are moving around. This combination of automated and manual processes would require the implementation of stringent safety precautions. And this wasn’t the only challenge facing Linde MH; the ambitious project would also have to be delivered during ongoing operation.
Since the go-live, the way our employees work has also changed. Instead of seeing automation as competition, they now understand that it provides valuable support. In other words, instead of machines replacing people, machines have enhanced their skills and expertise
Simone Gedda, Logistics Manager at Madi Ventura
From Concept to Completion
As general contractor, Linde MH started by designing a new warehouse layout. This design was then used to create a new high rack warehouse with ten aisles and six storage levels, which gave their client around 4,000 additional pallet spaces. Two automated Linde K-MATIC narrow aisle trucks now maximize the productiveness of the plant which is not accessible to people. They can lift loads of up to 1,500 kilograms to a maximum height of 16 meters, making them the ideal choice for Madi Ventura. Another bonus is that the industrial trucks use an intelligent natural feature navigation system to maneuver in the narrow aisles, with no additional floor tracks or laser reflectors required. The upstream and downstream logistics processes—in other words, goods supply and transport—are handled by five Linde L-MATIC AC pallet stackers. These trucks are also equipped with cutting-edge safety systems that use cameras and lasers, and can handle a total capacity of 39 pallets an hour. The transport routes for the automated equipment are based on data from the in-house warehouse management system and specified in advance via the Linde Robot Manager.
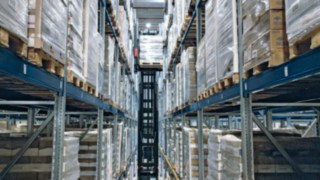
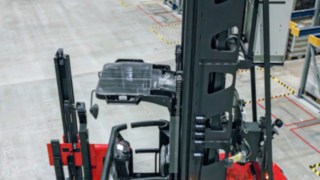
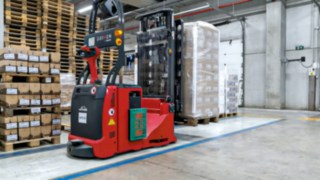
Success on Many Levels
Since the project was implemented—during ongoing operation, as promised—Madi Ventura have really reaped the benefits. Nowadays, 98 percent of all orders are handled flawlessly by the Linde automation solutions, even for peak quantities of 150 tonnes of goods daily. At the same time, the company can now operate with around 8,000 pallet spaces, up from the previous 4,000, without having to open up new areas for that purpose.
Significant value is also added by the data collected by the automation solutions; they help Madi Ventura to maintain a detailed overview of processes and identify further optimization potential.
But the benefits go beyond just the technical and monetary aspects: “Since the go-live, the way our employees work has also changed. Instead of seeing automation as competition, they now understand that it provides valuable support. In other words; instead of machines replacing people, machines have enhanced their skills and expertise,” is the verdict of logistics manager Simone Gedda.
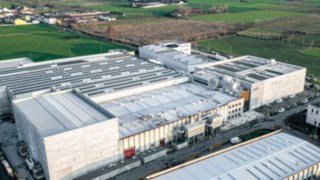
Madi Ventura S.p.A., Chieve (Italy)
In 1936, Attilio Ventura, a Genoa-based importer of fruit, vegetables, nuts and dried fruits, founded the company bearing his name Ventura . The company built up a national and international reputation over the next few decades, before merging with Milan-based Madi in 2000. Madi Ventura now has more than 90 suppliers from 30 different countries and is a top player in the steadily growing nuts, dried fruits and similar products sector.