Endurance testing of the Linde Xi20 P at Klingele Paper & Packaging
Top performance in a smart package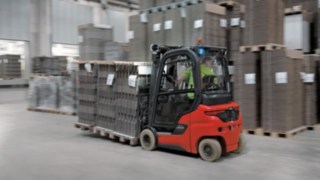
Lightweight products can be rather heavy-going. The logistics team at Klingele Paper & Packaging would certainly agree with this statement because the lightweight products they handle at their corrugated cardboard factory in Delmenhorst are a daily challenge for the team and their forklifts. Getting stuck into this challenge is the new Linde Xi20 P with fully integrated Li-ION battery.
While corrugated cardboard may be a relatively straightforward product, the operations taking place to move goods around the Klingele Paper & Packaging factory in Delmenhorst are anything but. “Our warehouse technicians here in the finished goods warehouse can sometimes spend seven and a half hours of an eight-hour shift sitting in their forklifts,” says Logistics Manager Nicolai Leese, giving an initial insight into the challenging work involved. The company has been producing items such as corrugated boxes at the site since 1955. These are then used as secondary packaging by companies such as dairies and animal feed manufacturers. Demand for these packaging products is so great that 1,500 pallets have to be moved and 60 to 80 trucks loaded with goods within a 24-hour period. This makes the company the ideal candidate to test the all-new high-performance forklift that it has been putting through its paces since mid-2024: the electric Linde Xi20 P.
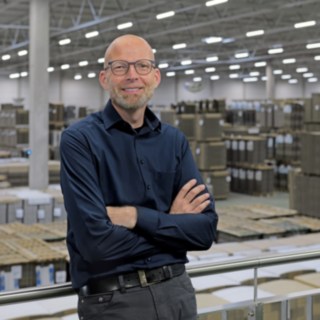
There is no room for compromise here when it comes to the forklifts: we need speed, agility, power and endurance.
Nicolai Leese, Logistics Manager, Klingele Paper & Packaging, Delmenhorst, Germany
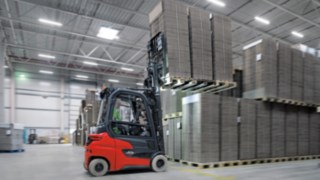
Chaotic storage principle calls for top performance at all times
Let’s break it down a bit further. The logistics team in the outbound warehouse at Klingele has two main jobs. “The first priority is to continuously transport goods from production to temporary storage. This is always done by one operator per shift, and we add others depending on the workload. The other colleagues take care of the order picking. The transport jobs are assigned via RFID terminals inside the forklifts,” explains Logistics Manager Nicolai Leese. Warehousing is carried out using the chaotic storage principle. “Automated high rack warehouses are often used in our industry,” says General Manager Patrick Ginter, adding: “However, a chaotic, RFID-supported block warehouse gives us significantly more flexibility, provided you can count on powerful, reliable and, above all, available forklifts.”
Electric forklift trucks with Li-ION technology have been used as standard for some time
Initially, lead-acid trucks were still in service in the finished goods warehouse in Delmenhorst, but the company has now switched over completely to lithium-ion forklift trucks from Linde Material Handling. “In the past, three lead-acid batteries had to be kept available for each forklift: one for driving, one for charging and one that was cooling down. Getting away from that was a blessing for us, not only because of the impressive availability that we can easily achieve through the combination of regular interim charging of the Li-ION forklifts and a backup truck, but also because of the constant power output and the improved occupational health and safety thanks to the much easier handling. In short, the lithium-ion forklifts simply perform a lot better,” explains Logistics Manager Nicolai Leese.
Linde Xi20 P: What makes this electric forklift so exceptional?
The keyword “performance” brings us back to the Linde Xi20 P mentioned at the beginning. ”In terms of design, we have a completely new truck concept here, which is designed for maximum performance and continuous operation – both of which are needed for the flow of goods at Klingele,” says Stephan Pleus from Linde network partner Willenbrock Fördertechnik, based in the German city of Bremen. This is mainly achieved by a clever combination of Li-ION battery, 90 V technology and recently developed synchronous reluctance motors. The latter also have an innovative heat management system, which means that the power units always operate at the ideal temperature, even when permanently subjected to extreme loads.
Where performance meets stability & agility
It not only sounds good on paper but the reality is also just as good after three months of field testing with the Linde Xi20 P prototype: “The Linde Xi has plenty of pep. The changes of direction happen very quickly and even when cornering it moves extremely swiftly,” says Shift Coordinator Walter Lazar. Warehouse worker Matthias Harms can also confirm the forklift truck’s excellent stability: ”We sometimes drive around with three pallets on our forks, but even with these kinds of loads, the Linde Xi remains stable at all times; you feel absolutely safe.” This balance of stability and manoeuvrability is partly achieved by the Linde combi-steering axle. It is thanks to this that the Linde Xi20 P, currently being tested at Klingele in its four-wheeled version, delivers almost the same manoeuvrability as the three-wheeled version with the swivel axle, which is also available.
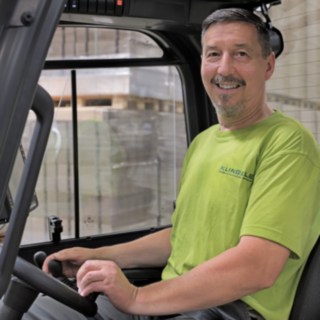
The Linde Xi20 P drives almost a bit like a go-kart with fork prongs.
Walter Lazar, Shift Coordinator, Klingele Paper & Packaging, Delmenhorst, Germany
The Linde Xi20 P is also in a class of its own in terms of space & comfort
The Linde Xi20 P scores additional points with the Klingele team for its excellent lifting and lowering performance, which is 20 percent above the industry average. Unlike conventional electric forklift trucks, the battery in the Linde Xi models is permanently integrated into the forklift. As this eliminates the need for the battery tray that features in other models, It has been possible to position the (now larger) entry step lower and redesign the operator’s workstation.
Warehouse Technician Thomas Lüssen – all 2.04 metres of him – reports: “I have significantly more headroom inside than in my previous forklift. And the footwell is also bigger, even though the forklift itself is more compact. I think it’s great!” The low-vibration driving experience also received a lot of praise. In addition to the air-sprung operator’s seat, this is achieved through special elastomer ring bearings, via which the mast, drive axle and steering axle are decoupled from the chassis.
Our warehouse floor is fairly new, but there are still some bumps. This is no problem for the Linde Xi20 P. It takes everything in its stride.
Thomas Lüssen, Warehouse Technician, Klingele Paper & Packaging, Delmenhorst, Germany
The verdict: the Linde Xi20 P is spot-on when it comes to customer requirements
A satisfied team, impressive handling performance and high availability: given this interim verdict, it is little wonder that the managers at Klingele consider the Linde Xi20 P prototype the perfect fit for their industry.
General Manager Patrick Ginter gives his initial review: “We are already convinced of the merits of Li-ION technology because of what it delivers in terms of performance, handling and sustainability. With the Xi models, Linde Material Handling has now brought to the table a forklift truck concept that really is ideally suited to our specific requirements – above all in terms of the speed and continuous operation we require.”
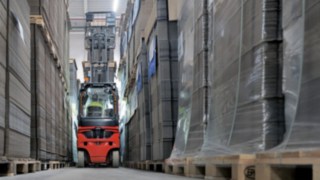
Klingele Paper & Packaging
Klingele Paper & Packaging is one of the largest manufacturers of corrugated raw paper cardboard and corrugated cardboard packaging in Germany. From its Delmenhorst factory, the company supplies customers across northern Germany, Denmark and the Netherlands with high-quality corrugated boxes, die-cut packaging and pre-glued folding boxes in a wide range of sizes. Various industrial trucks from Linde Material Handling are used for the internal product flow processes at the site, including seven Linde E20 with Li-ION batteries. For optimal, uniform control of the charging currents without load peaks, the company also relies on the Linde connect:charger. Bremen-based Linde network partner Willenbrock Fördertechnik is responsible for servicing and maintaining the fleet.