Linde automation fulfils the highest flexibility requirements
Where there's an obstacle, there's also a way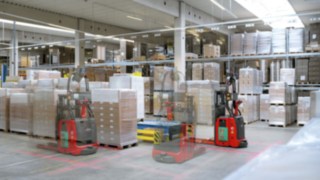
The most fascinating equations are known to be the ones with multiple unknown variables. One such variable was to be found in the ‘Automation’ chapter of the Requirements Specification from paper specialists Franz Veit. How can the transportation tasks be reliably handled in a production and warehousing environment whose face is constantly changing?
Today in the supermarket, tomorrow at a child’s birthday, the next day at a newsagents and on Saturday at the football stadium? When you hold a Franz Veit product in your hand, then that is what you are holding, but one way or another, given all the till receipts, deposit receipts, paper streamers, rolls of lottery tickets and so on that Europe’s leading manufacturer produces, pretty much everyone will have come into contact with them at some time. Which makes it all the more remarkable that all of these (and some 4000 other products!) are produced on one and the same site.
It’s an enormous output, and the logistics have to keep up.
Hirschaid bei Bamberg, Germany. Ever since 2006, the production machines here have been running Mondays to Fridays in three-shift operation practically around the clock. “Before moving out of town, our production site was in the centre of Hirschaid and was close to bursting at the seams. And although over here, with an area of 36,000 square metres, we’re not exactly pushed for space, there’s hardly a corner that goes unused,” says Managing Director Christoph Ettel (r. in photo) as he takes us on a tour of the hall complex. “If there’s something we don’t have, it’s down to space,” continues Authorised Officer Daniel Werner (l. in photo). “All the same, we process about 200 tonnes of raw paper every day into a vast range of different products that then get dispatched as quickly as possible.” In the midst of all of this at Franz Veit is a chaotically organised intralogistics system which the company, primarily for reasons of added value, wanted to optimise, or at least partially automate.
If you’re boxed into a corner...
Rolls of material above head height in front of production machinery, packed pallets and boxes as far as the eye can see, with packing robots and production equipment scattered in between ... it’s not exactly the dream environment for automated transport processes. “But that’s exactly what we were dealing with,” says Daniel Werner emphatically, referring specifically to the route from Production Dispatch to Stretch Wrapping Machine Supply in the neighbouring part of the hall. “Our people used to pick up the finished goods from the paper processing machines, bring them to the stretch wrapping machines on a forklift and wait for them to be film wrapped before carrying on,” explains Werner. A suboptimal process, especially for the early shift, where the first task was to clear up to 150 pallets from the previous shift. “That alone kept six people occupied for about two hours,” relates Werner.
... you first have to think outside the box
Situation: unsatisfactory. Solution: challenging. Daniel Werner reports: “OK, so we have the same transport processes over and over again, but we also have a production and warehousing environment that’s constantly changing.” Which in turn means that any automation system needs to be able to keep up with such a high degree of flexibility and ‘organised chaos’. AGV systems that needed mirrors or guide rails were thus out of contention from the start. “We were in discussions with a lot of suppliers. But our required solution needed to function like you see with a robot vacuum cleaner. You put the machine in the space, it orientates itself automatically and gets on with its work, even when an item of furniture moves around occasionally,” explains Daniel Werner. “This was something where only the Linde MH network partner Ernst Müller Fördertechnik could help us.”
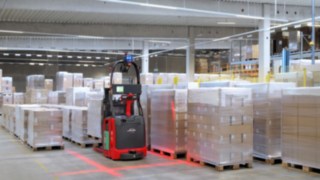
Automation, Brand: Simple
The idea from the Linde professionals, of using two autonomous Linde L-MATIC pallet stackers immediately found favour with the clients, especially as hurdles that had previously appeared insurmountable vanished pretty much into thin air. Thanks to their natural feature navigation technology, the machines can orientate themselves automatically in the space and require just a few reference points that can readily be adjusted in a digital mapping system. “That was exactly what we were looking for,” recalls Daniel Werner. There was the additional benefit that the Linde L-MATIC machines function without a platform and the pallets can be picked up directly from the floor. These were powerful arguments that prompted the decision-makers at Franz Veit to work with Ernst Müller on implementation.
Fluidity in practice
The two Linde L-MATICs now go about their work in Hirschaid as if they’d always been there. One vehicle is responsible solely for clearing the production machines. The machine operator places the pallet loaded with the finished goods at a predetermined collection point and calls the automatic Linde truck by pressing a button. The truck lifts the pallets, weighing up to 1000 kilos, and transports them safely around any obstacles into the neighbouring area of the hall to the stretch wrapping machine’s conveyor belt. Once the goods are wrapped, the second Linde L-MATIC takes over at the output point; it carries the pallet to the transfer point a few metres away, from where its human colleagues quickly move the goods to the specified quadrant for that order.
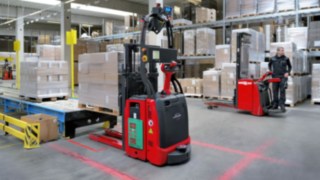
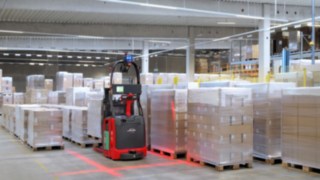
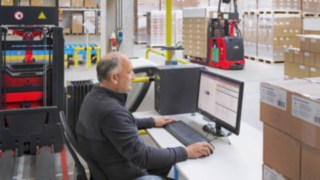
Division of labour included
Another reason why the interaction between human and machine works so perfectly at Franz Veit is that the technology on the Linde L-MATIC automatically identifies the spaces at the transfer point that are currently free, and fills them accordingly. An interesting detail: at midnight every night, the Linde L-MATICs swap jobs. According to Daniel Werner, “since the two work ranges are very different, this allows us to balance up the workloads.” Charging up the Li-ION batteries is equally convenient: when the battery level falls below a specified threshold, the Pallet Stackers navigate themselves automatically to the charging station.
Linde technology masters the chaos
Watching the tireless operation of the L-MATIC duo in Hirschaid, it quickly strikes you that nothing fazes the pair of them. This is something that Authorised Officer Daniel Werner can readily confirm: “The machines have been operating now since November 2021. Ideally I’d have a time-lapse camera so I could show you how frequently our production and warehousing environment has changed since the start of the project. What’s here today is over there tomorrow – machine A moves to location B and so on. That’s never been a big issue for the Linde L-MATICs, up until now they’ve always found their way without a problem.”
The output of the Linde machines has exceeded my expectations in every respect.
Daniel Werner, Authorised Officer at Franz Veit
Production dispatch at a record level
What is really impressive, though, is the output achieved by the automation project. Guaranteed performance is currently being exceeded by nearly 50%. “The present record for the number of pallets that the trucks have cleared from production is 298 in 24 hours,” relates Daniel Werner happily. Little wonder then, that the paper professionals are already considering expanding automation into further process steps, for example by putting the production machines in a position where they can call the Linde L-MATICs for themselves. “We want to think constructively about this; another factor is that automation enjoys a high degree of acceptance among the staff, because we’ve shown our people right from the start that the machines are not taking work away from them. Rather, they are allowing them to concentrate on other more important activities,” stresses Managing Director Christoph Ettel. He continues, “I’d say we get on very well with this distribution of roles.”
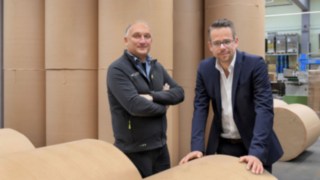
The company Franz Veit GmbH is a leading European producer of till and ticket rolls, paper streamers, confetti and other paper and film products. The business, whose roots can be traced back to 1906, today has some 190 employees. The production site in Hirschaid bei Bamberg in Germany, built in 2006, is the most modern factory of its kind in the world, and with an area of 36,000 square metres it is also the largest. For intralogistics, the paper specialists have long relied on technology and expertise from Linde Material Handling. The Linde MH network partner Ernst Müller Fördertechnik is responsible for service and customer care.